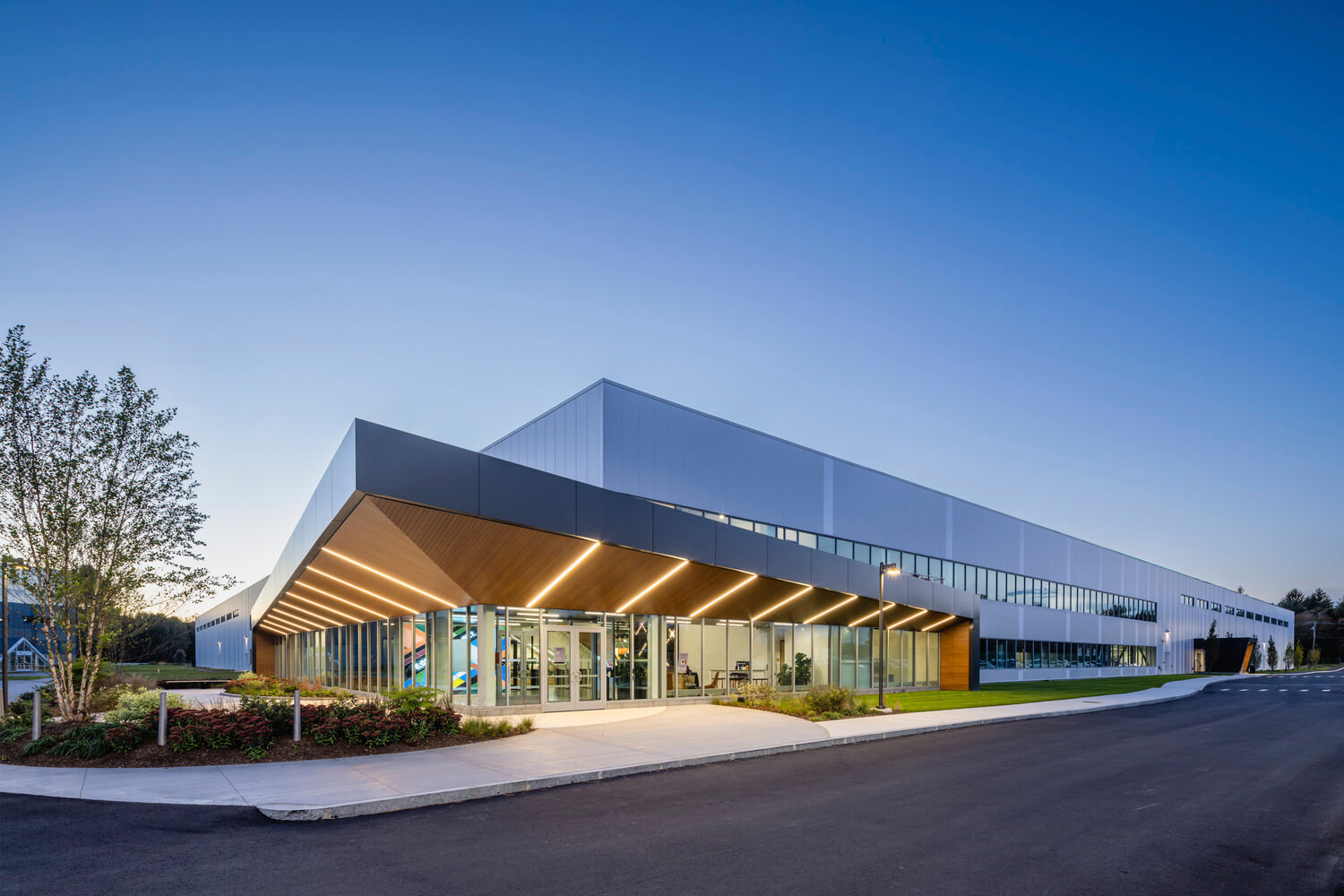
In 2017, developers Atlantic Management purchased a 66-acre pharmaceutical campus in Westborough in Greater Boston’s MetroWest area. The previous owner, AstraZeneca, had recently vacated the site, leaving the Town with reduced tax revenue and a piecemeal mix of empty drug manufacturing plants, offices, and recreational facilities.
Today, the now-fully-redeveloped site has found a second life as a high-tech industrial hub for Amazon’s world-leading robotics business. The campus has since been expanded to include a second facility and a distribution center, both tenanted by Amazon.
Benefitting from SMMA’s suite of services—from architecture and engineering to permitting, landscape architecture, civil engineering, and sustainable design—Atlantic Management tailored the site to Amazon’s demanding program in the face of ever-shifting business demands. The result is a sustainable, thoughtfully designed campus that serves as a model for developers and landlords operating in New England’s growing light-industrial market.
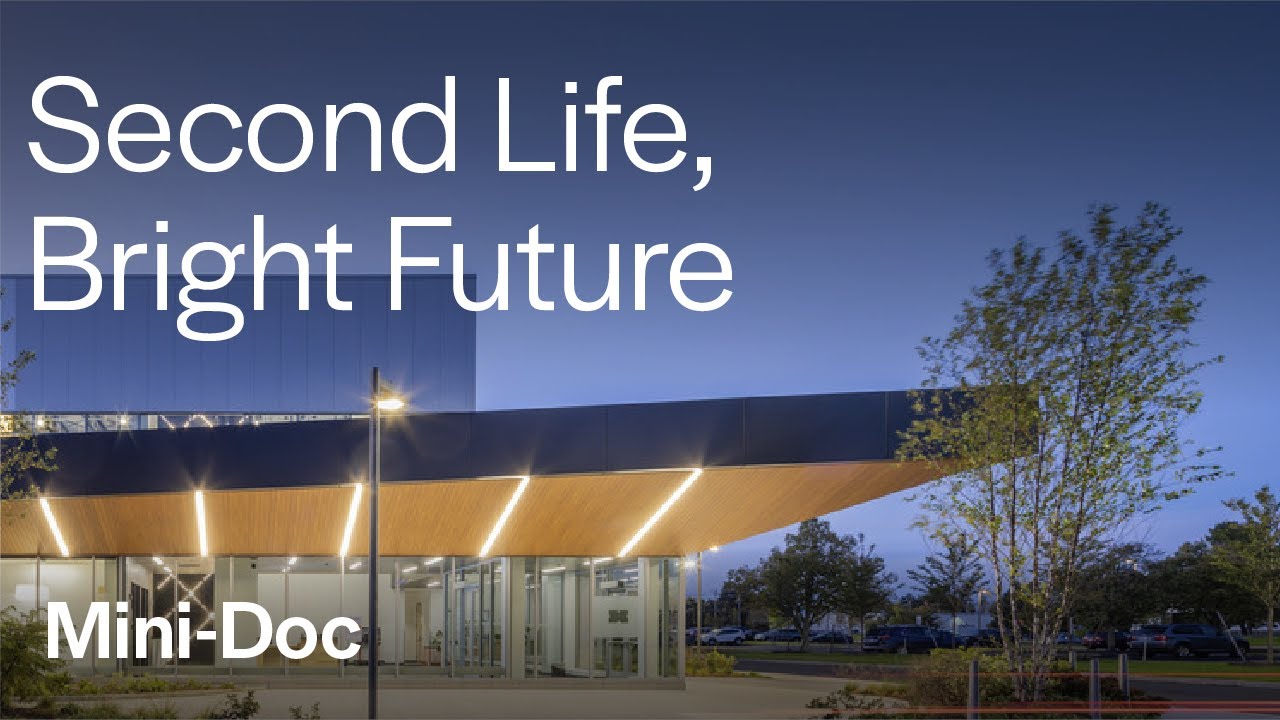
Located 30 miles west of Boston, the site offered three key features that would likely attract a large corporate tenant: 35 acres of developable land for new buildings, parking, and amenities; a mature landscape of trees, meadows, and trails; and quick access to Route 9 and the Boston-to-Worcester commuter rail.
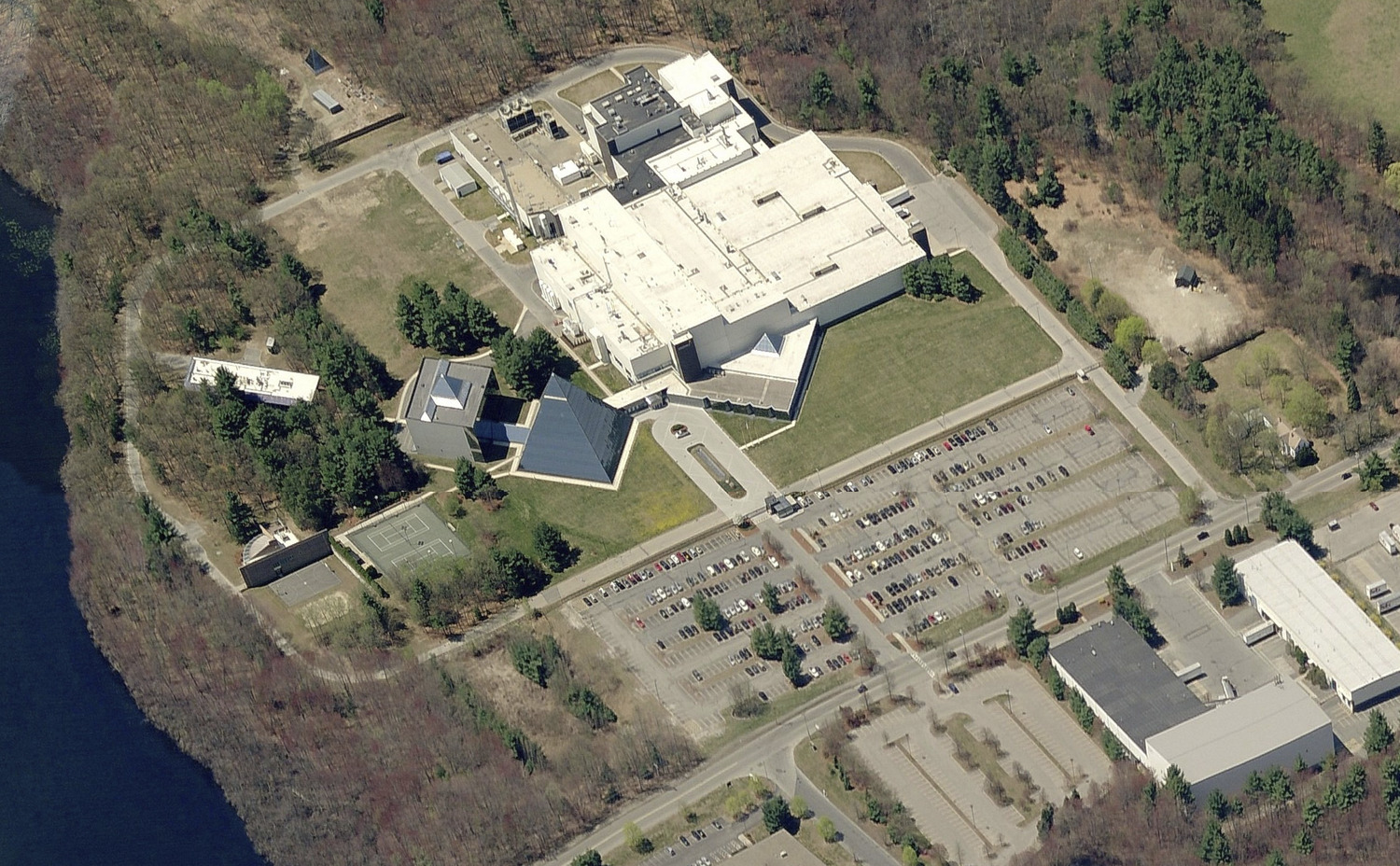
Scouting the site
Before purchasing the property, Atlantic Management hired SMMA to scout the site and perform test fits to determine its true value. “They wanted to see its capacity and check for any red flags, such as wetlands or a limited building area,” said Michael Pardek, lead designer for the project. “Then they could make the most competitive offer.”
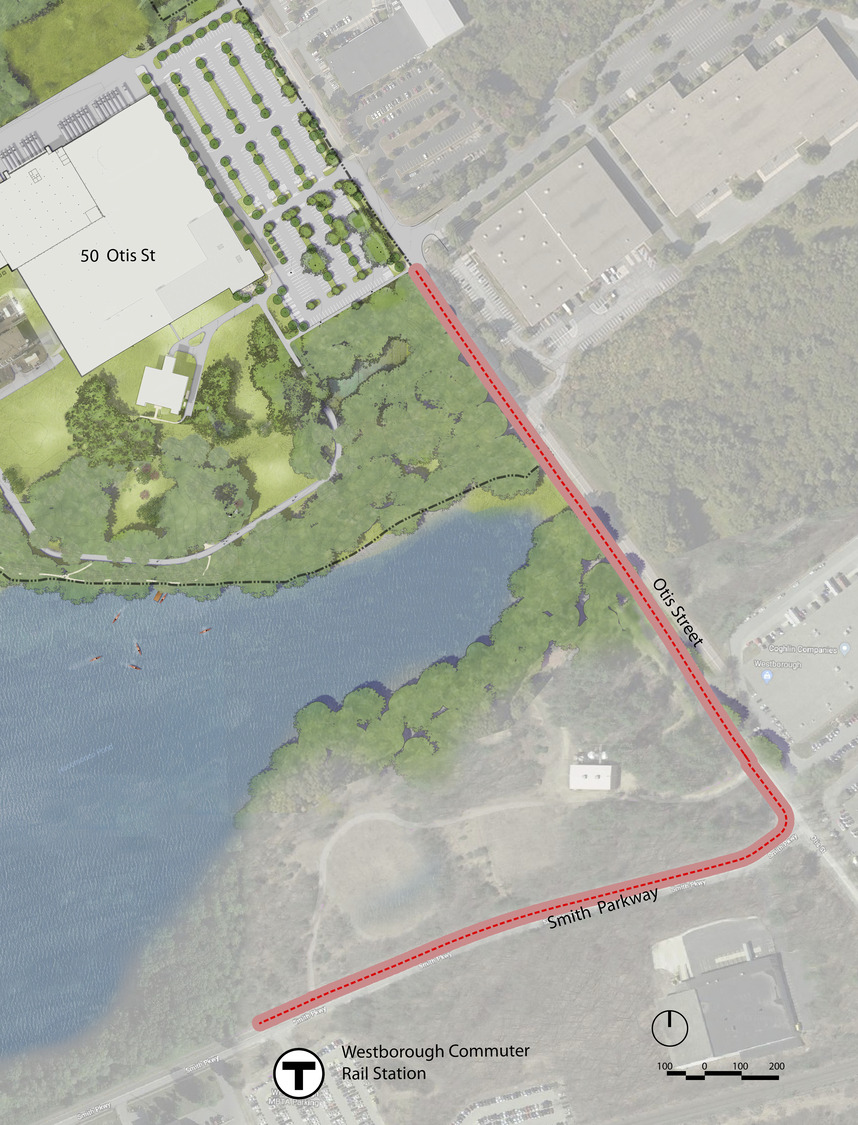
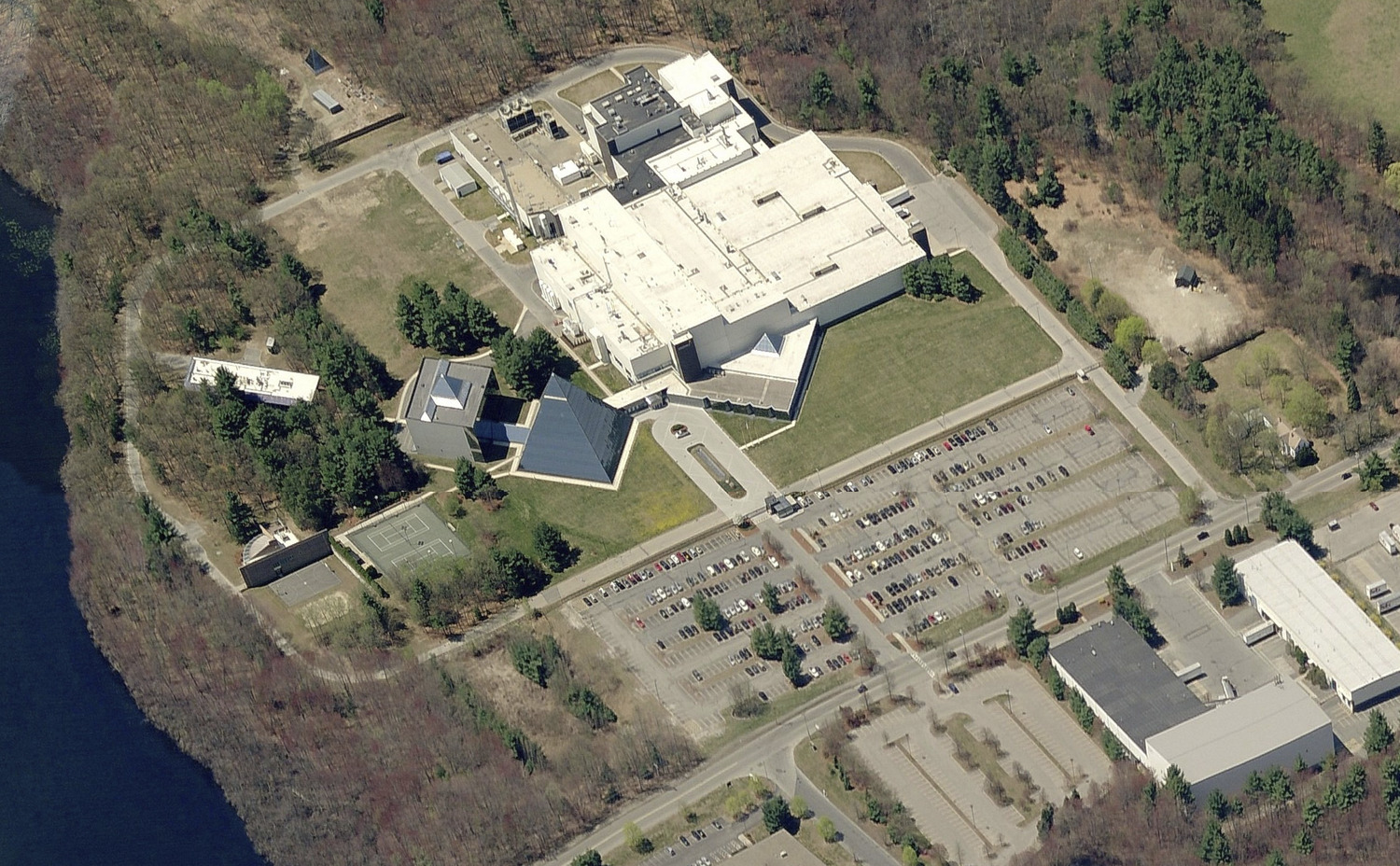
Scouting the Site
Before purchasing the property, Atlantic Management hired SMMA to scout the site and perform test fits to determine its true value. “They wanted to see its capacity and check for any red flags, such as wetlands or a limited building area,” said Michael Pardek, lead designer for the project. “Then they could make the most competitive offer.”
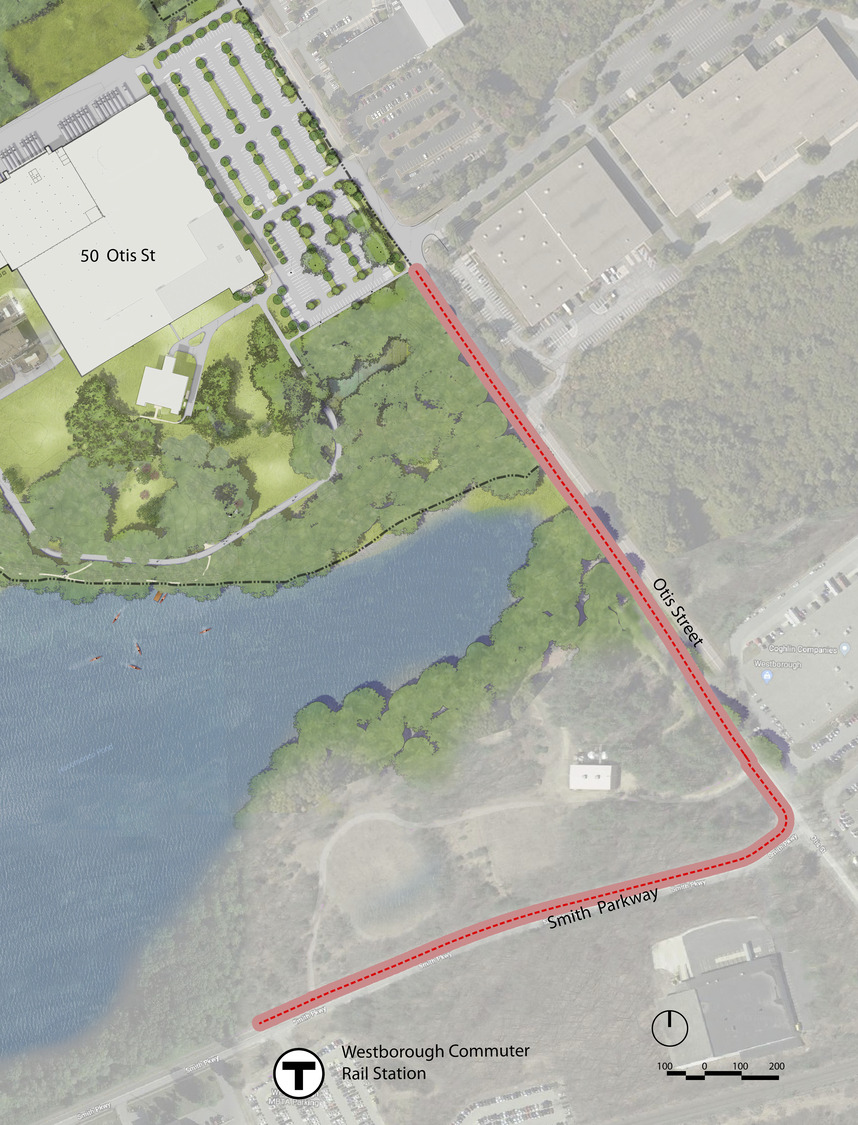
Located 30 miles west of Boston, the site offered three key features that would likely attract a large corporate tenant: 35 acres of developable land for new buildings, parking, and amenities; a mature landscape of trees, meadows, and trails; and quick access to Route 9 and the Boston-to-Worcester commuter rail.
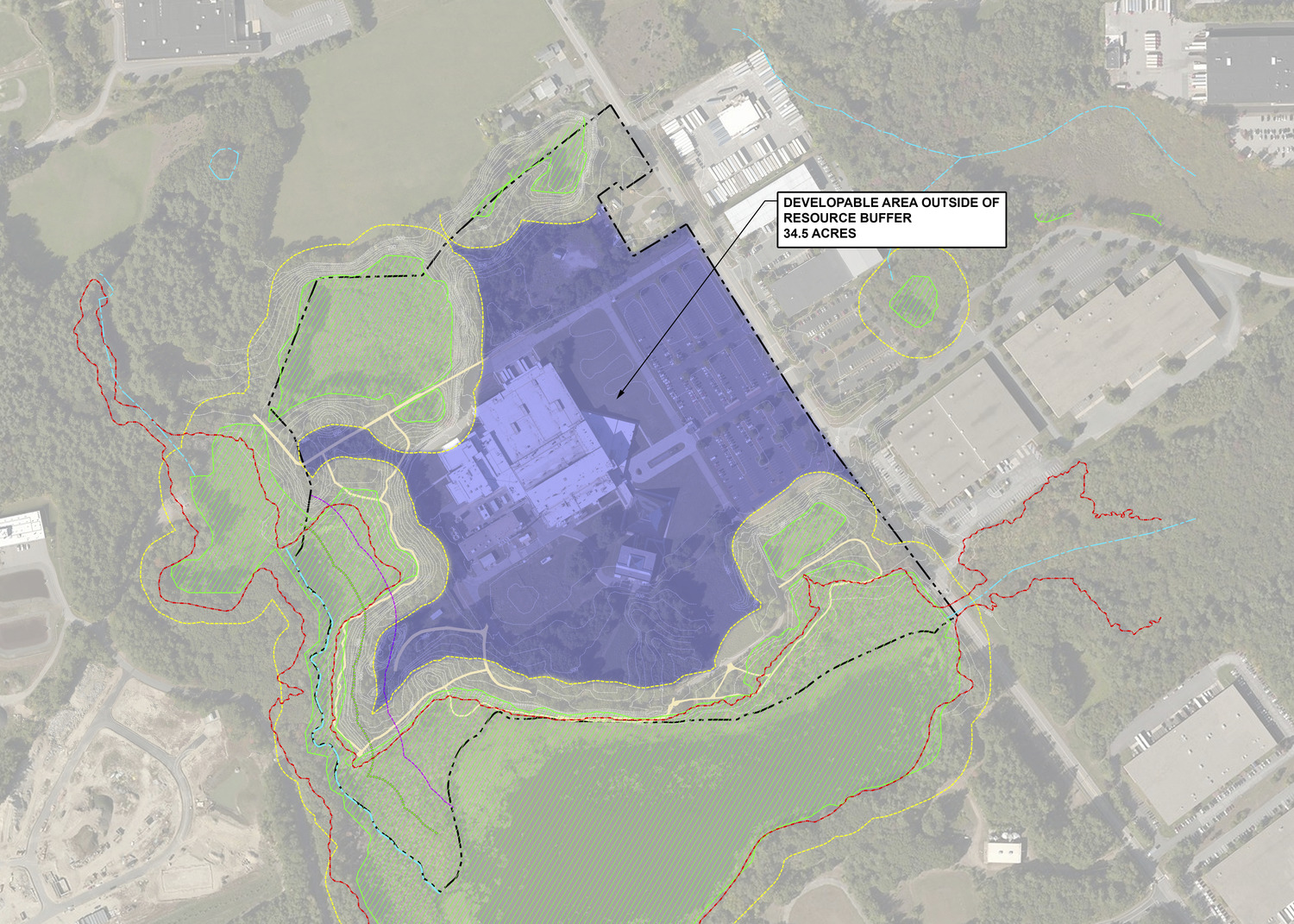
“SMMA helped us tremendously in understanding what we had out there. Not just that, but what we could do with it in terms of expansion. We had various scenarios for different people, because we had a lot of great companies come through that space.”
John Sullivan, Senior Vice President of Development & Construction, Atlantic Management
The design team initially sought to preserve much of the old AstraZeneca campus, which had been geared toward the production of two specific drugs. One test fit proposed a new life science campus with lab and office buildings; another a large manufacturing facility. Both reflected the type of tenant Atlantic Management was eager to court: large, innovative firms with manufacturing or research needs and a desire to tap into the high-skilled workforce in the MetroWest area.
An early test fit for a large manufacturing plant that preserves the original warehouse.
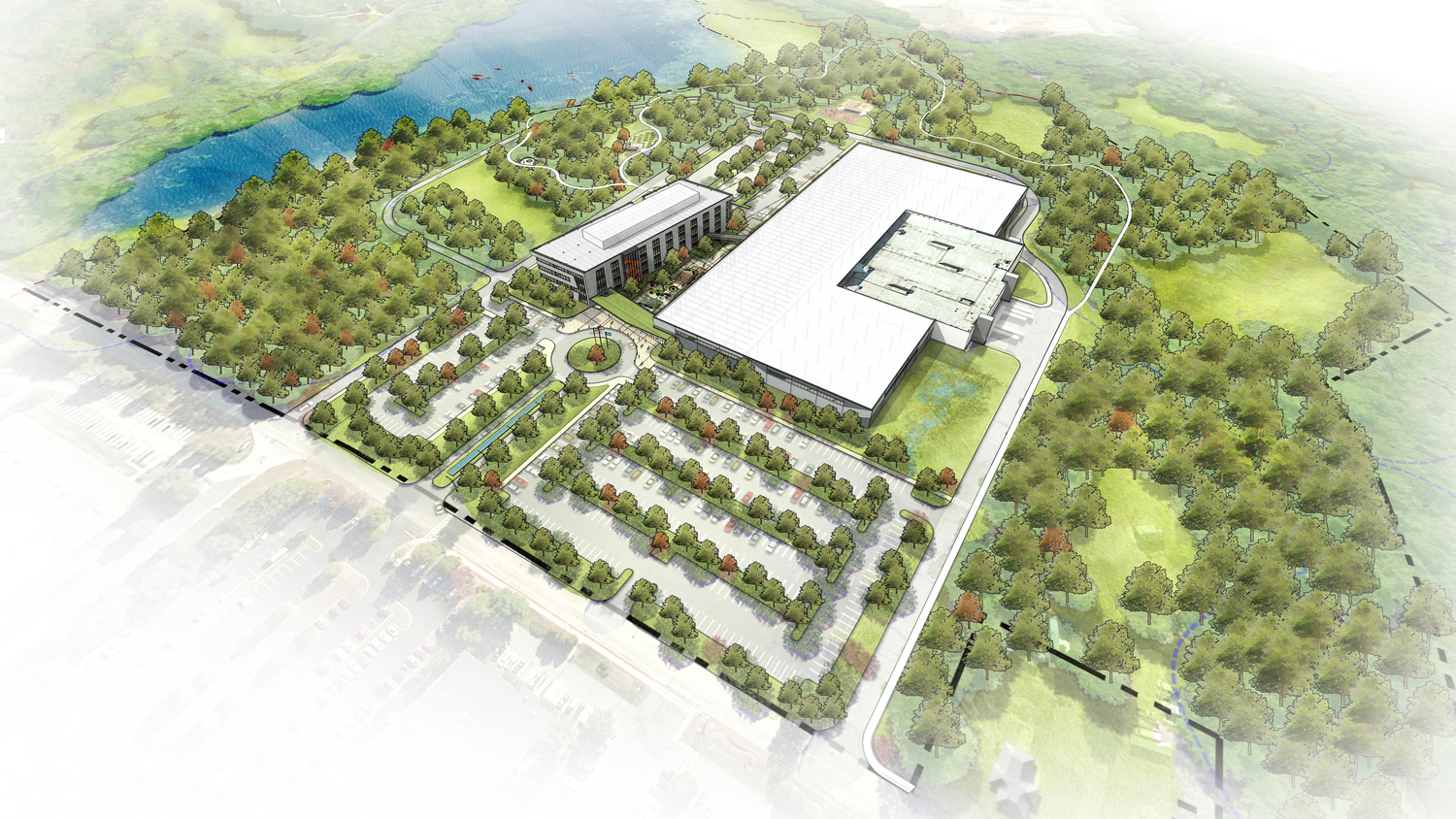
“By doing the test fits, we came to the conclusion that only two [existing] structures were actually marketable to new tenants,” said Pardek. The buildings in question were a 64,400 square foot warehouse, and an office building known as “The Cube”. In the end, both buildings were to form a crucial part of the final development.
Even after purchasing the site, Atlantic Management were unsure of the exact direction the development would take. But as a likely tenant emerged—a global tech firm in need of a large industrial space—they made the call to demolish most of the existing campus and start over.
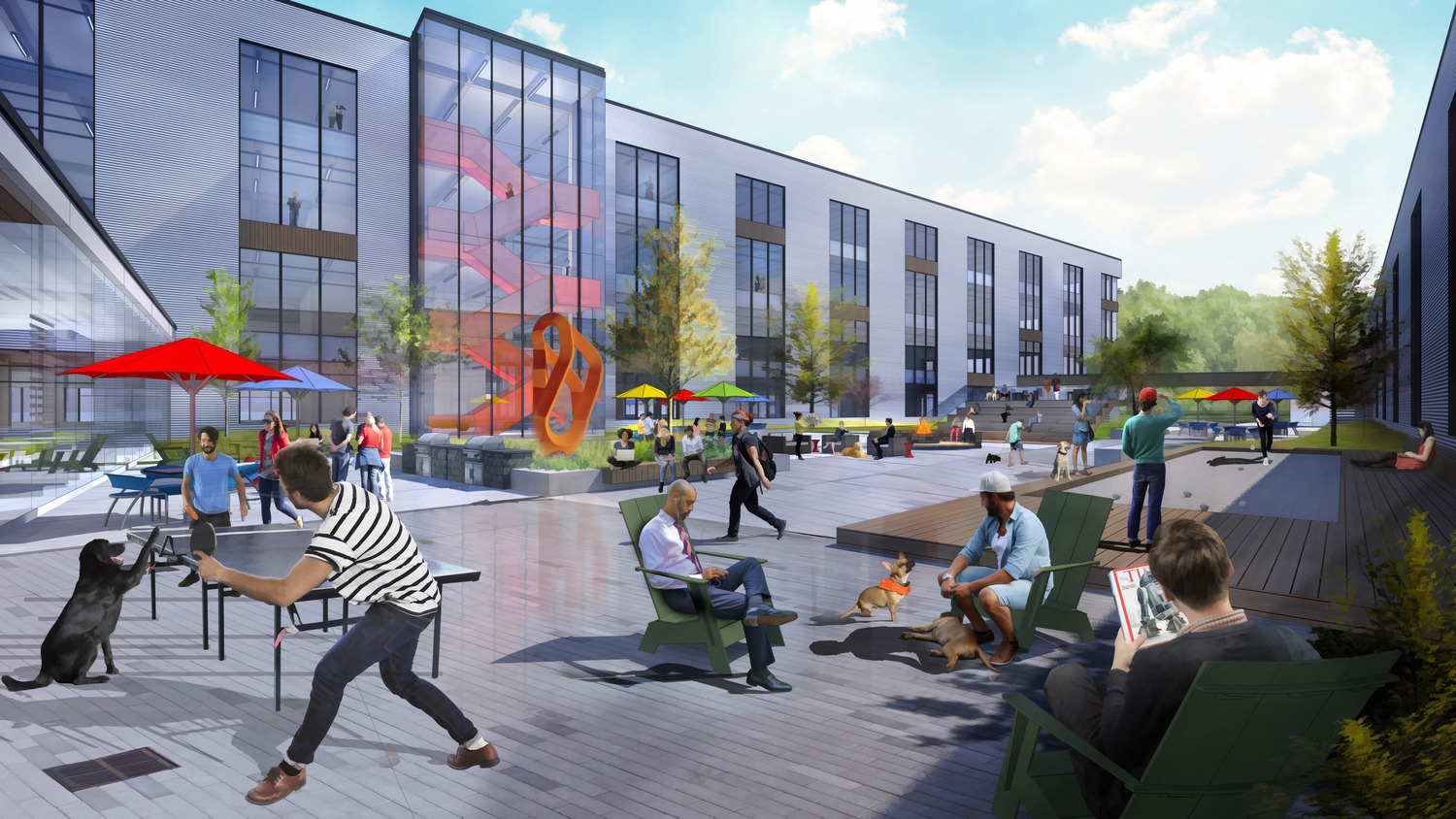
The potential for further development was another selling point. “We wanted to show the tenant that the site had a lot of flexibility, a lot of development potential, and that you could expand beyond the first phase,” said Pardek. To this end, SMMA created several industrial design concepts tailored to Amazon’s program, including landscaping, trails, and recreational facilities. The designs emphasized the large amount of parking available—a dealbreaker for the tenant.
Winning over a community
While SMMA and Atlantic Management had worked together on projects going back two decades, the two firms had not collaborated in Westborough. The team knew that community engagement would be key to getting the project off the ground.
“Public outreach was very important in this project, and Atlantic Management understood that,” said Will Park, a civil engineer and permitting expert at SMMA. “Early outreach with the Town, including them as an integral part of the process—we knew these things would be crucial to the success of the project.”
Westborough’s financial picture lent a sense of urgency. “After AstraZeneca shut things down, the Town took a big hit with real estate taxes, personal property taxes, things like that,” said Sullivan. “So they were very committed to helping us find a tenant to get into that building, either as it existed or redeveloping it.”
Leaders from SMMA and Atlantic Management met with the Town’s planning board to lay out their proposed vision for the project. The headline benefits were an easy sell: tax revenue for a vacant site, high-end job creation, and a prestige tenant poised to sign.
But the proposed timeframe—a 14-month path to full occupancy with several overlapping design, demolition, and construction phases—was met with skepticism. The Town raised doubts as to whether the permitting process could be completed in such a short period. Other concerns included the condition of the existing utility infrastructure and the risk of disruption caused by the proposed retrofit.
To allay these fears, SMMA outlined a step-by-step plan for obtaining building permits for each of the project’s three phases. The plan involved “piggybacking” on much of the site’s existing utility corridors such as water, sewage, and drainage to minimize the risk of delays. The team also shared with the Town their expertise around sustainability and stormwater management, drawn from experiences working with Atlantic Management in similar projects in Massachusetts.
“We can’t say enough about the Town of Westborough in terms of helping us understand where we were going from a development standpoint,” said Sullivan. “And of course, they were ecstatic, because it’s bringing this top company into the town with great paying jobs, skilled workers, and really transforming that property to fit for Amazon Robotics.”
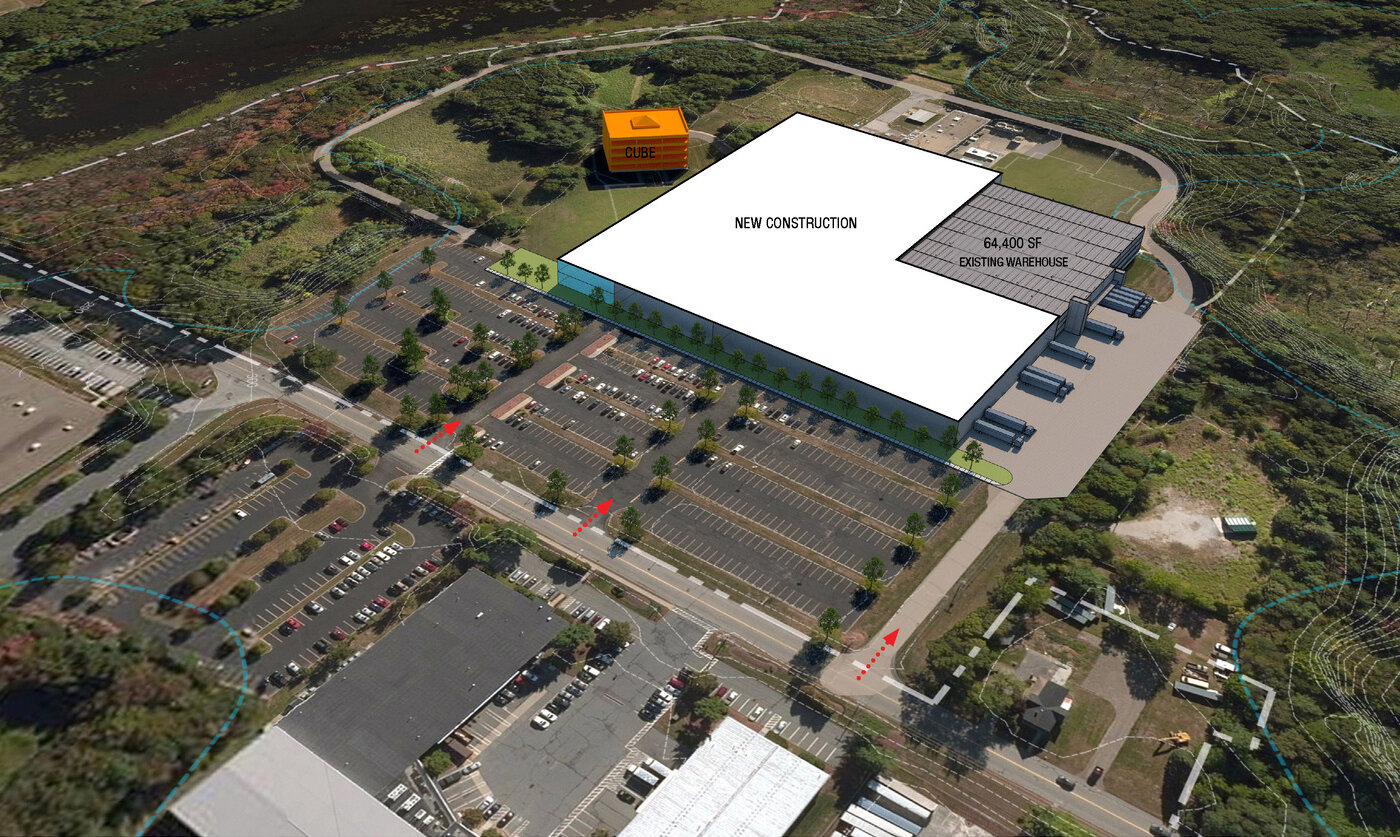
The Big Idea
With Amazon on board, SMMA and Atlantic Management unveiled their Big Idea: preserve the warehouse and The Cube, but greatly expand the warehouse footprint to form a 357,000 square foot robotics testing and production facility. This new “big box” would also include offices, a dining hall, roof deck, and outdoor landscaping.
The idea was well received by the new tenant, as keeping the warehouse and The Cube would allow for an early move-in. But after signing the lease, Amazon continued to push hard for an even quicker move-in and expansion. “Every day the tenant was delayed, they were missing out on hundreds of thousands of dollars of product rolling out the loading dock doors,” explained Park.
To solve this time-crunch, the team devised a 14-month path to full occupancy, carried out in three phases.
Phase One saw the tenant move into the remodeled Cube to begin their robotics testing, while demolition crews worked to clear the rest of the site, including the redundant “Pyramid”.
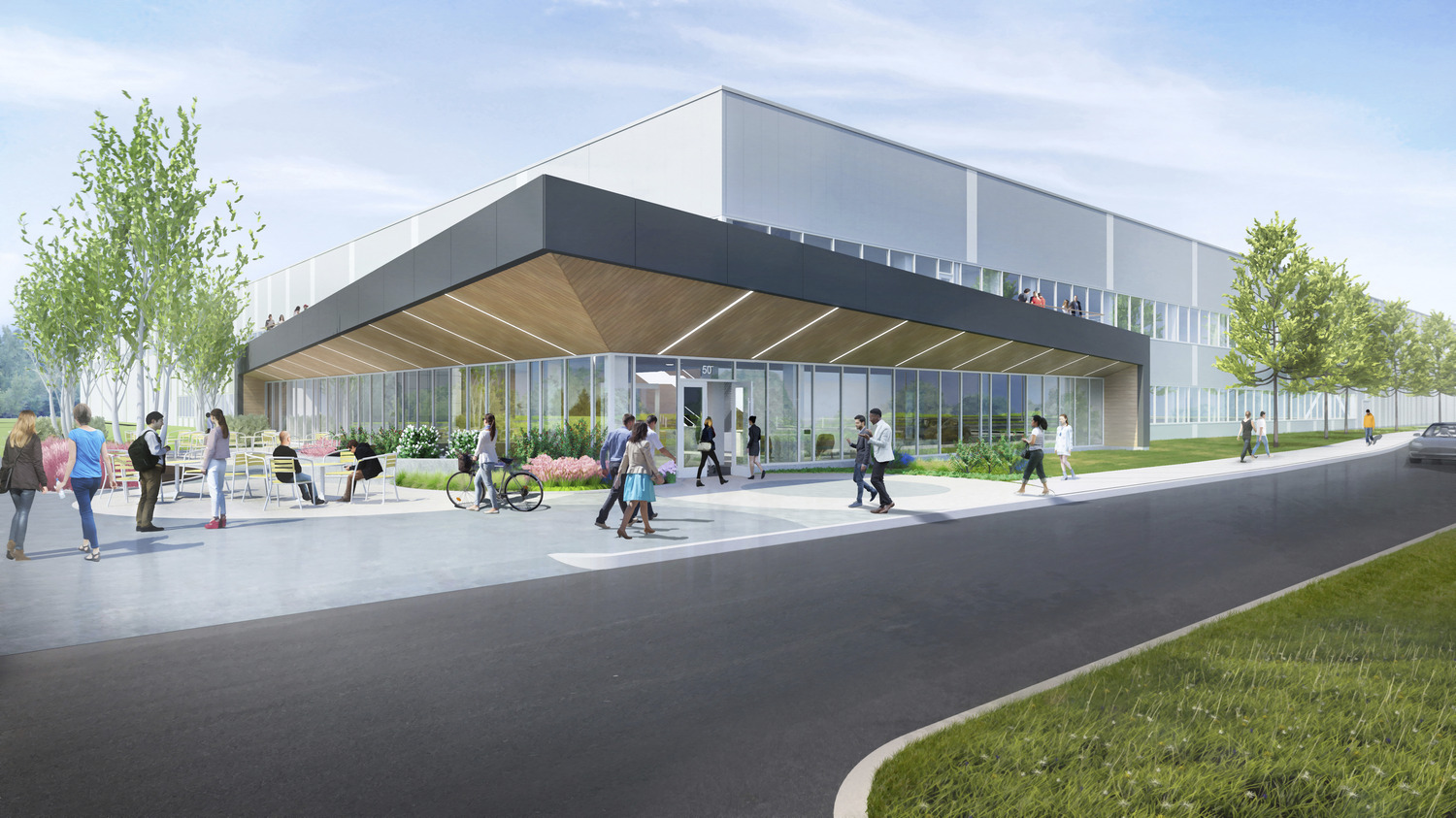
In Phase Two, Amazon migrated to the existing warehouse to expand their testing and production efforts. This move succeeded despite coinciding with the first COVID-19 lockdown in March 2020.
Phase Three—the giant new warehouse addition—proved the most challenging. “The need for more space was a constant pressure,” says Anthony Iacovino, an architect at SMMA. “Our challenge was to design the core and shell while tenant fit-ups and robotics testing work was still going on.”
With the design picture always shifting, SMMA sought to keep things flexible. The team worked with construction managers J. Calnan & Associates to explore speeding up the schedule by using a pre-engineered building. “Pre-fab works really well until you have to make a change, which slows everything down,” says Brett Wilkinson, a structural engineer at SMMA. “We shared our reservations with the client, and in the end, they opted against it.”
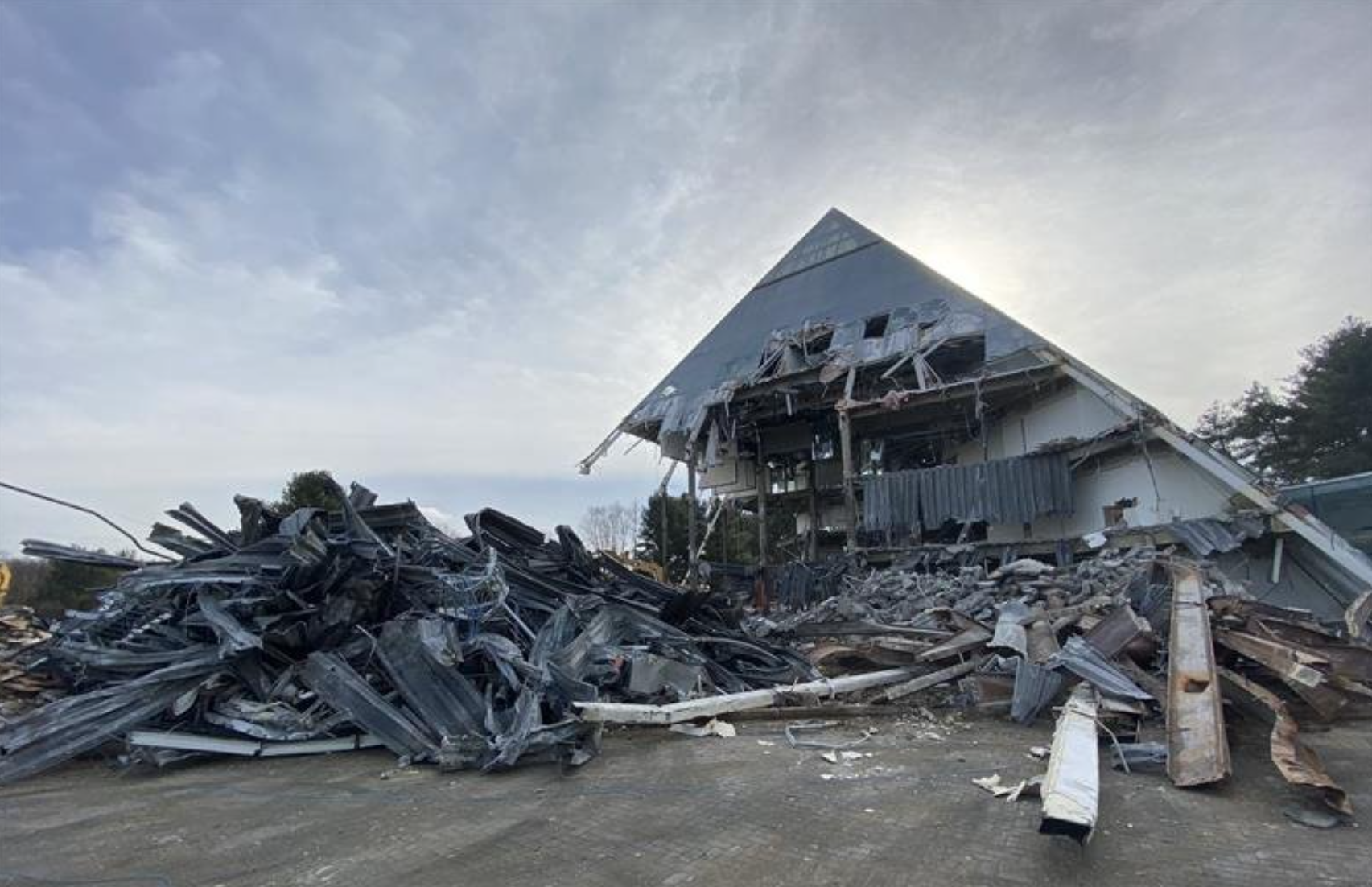
The move away from pre-fab allowed the project’s engineers to coordinate with tenant requests and adapt to the evolving architectural design. “We relocated base frames, aligned wall frames with the exterior metal panels, and adjusted for new MEP equipment locations,” says Wilkinson.
SMMA worked closely with IA Interior Architects, the tenant’s interior designers, to harmonize the team’s architectural, structural engineering, and civil engineering work with the proposed interior-fit-out.
“Because of how quickly we were hoping to get the tenant into the building, the most challenging piece was coordination between teams who were overlapping their work at different times,” says Grady Capobianco, Senior Development Manager at Atlantic Management. “SMMA worked really closely with AI to overcome those hurdles, which made the builders’ lives easier and our lives easier.”
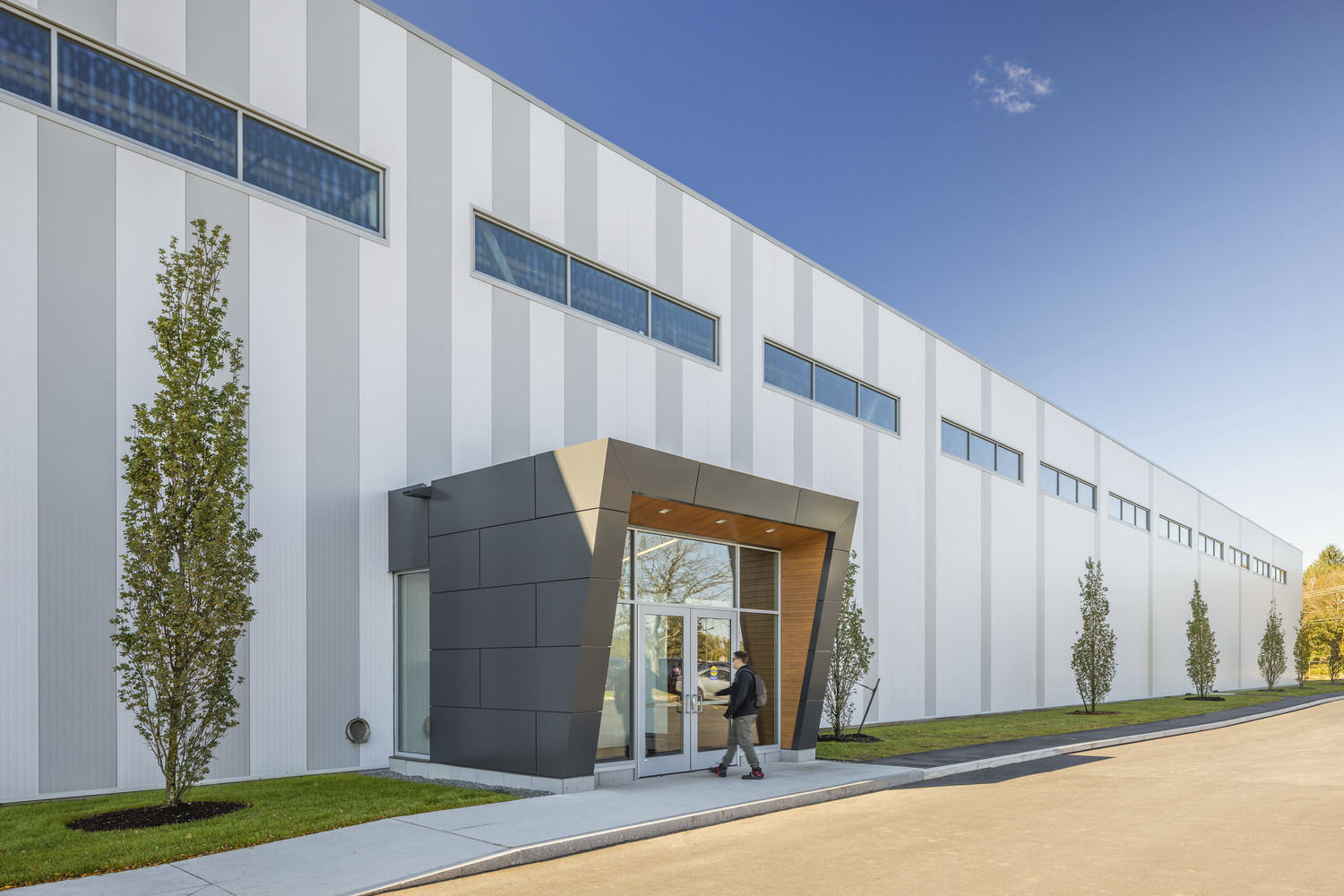
Sustainability on a budget
As part of the lease with Amazon, Atlantic Management committed to expanding the main building to 357,000 square feet—a huge space. This posed a challenge to SMMA’s designers. Could they minimize construction costs for the developer while also exceeding the state’s stretch energy code standards?
“The building envelope was all-important,” says Iacovino. “We used an insulated metal panel wall system on all sides of the building. The panels are made from low-cost and utilitarian materials that have been around for decades, but only now are we using them in a way that delivers better thermal performance.”
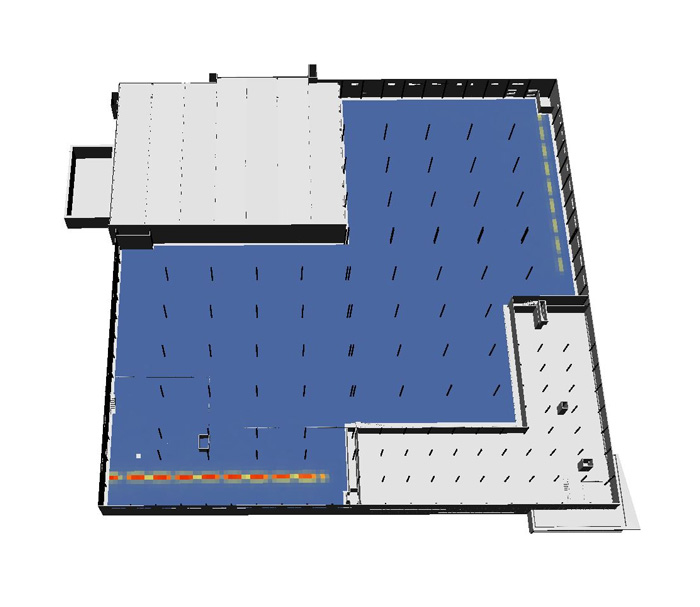
The team created energy models to test insulation thicknesses and mechanical systems options.
Results of energy modeling showed that, for the building to comply with state stretch energy codes, the insulated panels had to be at least four inches thick. The final design goes a step further: six inches of insulation on the roof, and four inches for the walls.
“Warehouse buildings 20 years ago were probably the least efficient building you could possibly build,” says Iacovino. “It was literally just a skin of metal, often with no insulation at all. This is very much the same assembly, but now we’ve got that nice, insulated panel. It may look the same, but it performs much better than those buildings ever did.”
The insulation, combined with a high bay window-to-wall ratio of just 5.2%, careful placement of windows, and huge solar PV-ready roof, maximizes the building’s energy performance. The project exceeds the state energy code baseline by 11.3%.
Seeing Daylight
Amazon sought to increase daylight into their new warehouse. But the obvious answer, adding skylights, clashed with the building’s thermal performance goals. “We found that the skylights were so cold compared to the roof assembly that you’re creating a roof that’s thermal Swiss cheese.” says Ethan Seaman, sustainable design analyst at SMMA.
Instead, the final design makes the maximum use of glazing in areas that are most beneficial to the building’s users, namely the office space, employee entrance and lobby, and dining areas.
15%
718, 543 kWh
Savings in Electricity
5%
5,177 therm
Savings in Fossil Fuel
11.3%
More efficient than stretch code
Up on the roof, over half of the total space—165,300 square feet—is given over to space for future solar panels. “We tried to angle the buildings as much as possible so that we had big wide stretches of roof with good solar orientation,” says Iacovino, speaking about 50 Otis Street and its all-electric sister buildings at 54 and 64 Otis Street. “We have the electrical infrastructure in place to take that power and make it. These are solar farms ready to happen.”
Rethinking “big box” architecture
The sheer size of the building gave SMMA’s architects a vast, empty canvas to explore. The team sought a design that would humanize the imposing box and create interest along its 2,000 linear feet of façade.
Simplicity was key. “How do we explore a façade with this really simple construction technique, simple windows, and make it into something more than you would expect?” says Pardek. “We worked with a gradient of color, from gray to white. It matches the idea that, as things get closer to the horizon, they get lighter. It’s an atmospheric perspective the eye normally takes in, and it occurs in nature.”
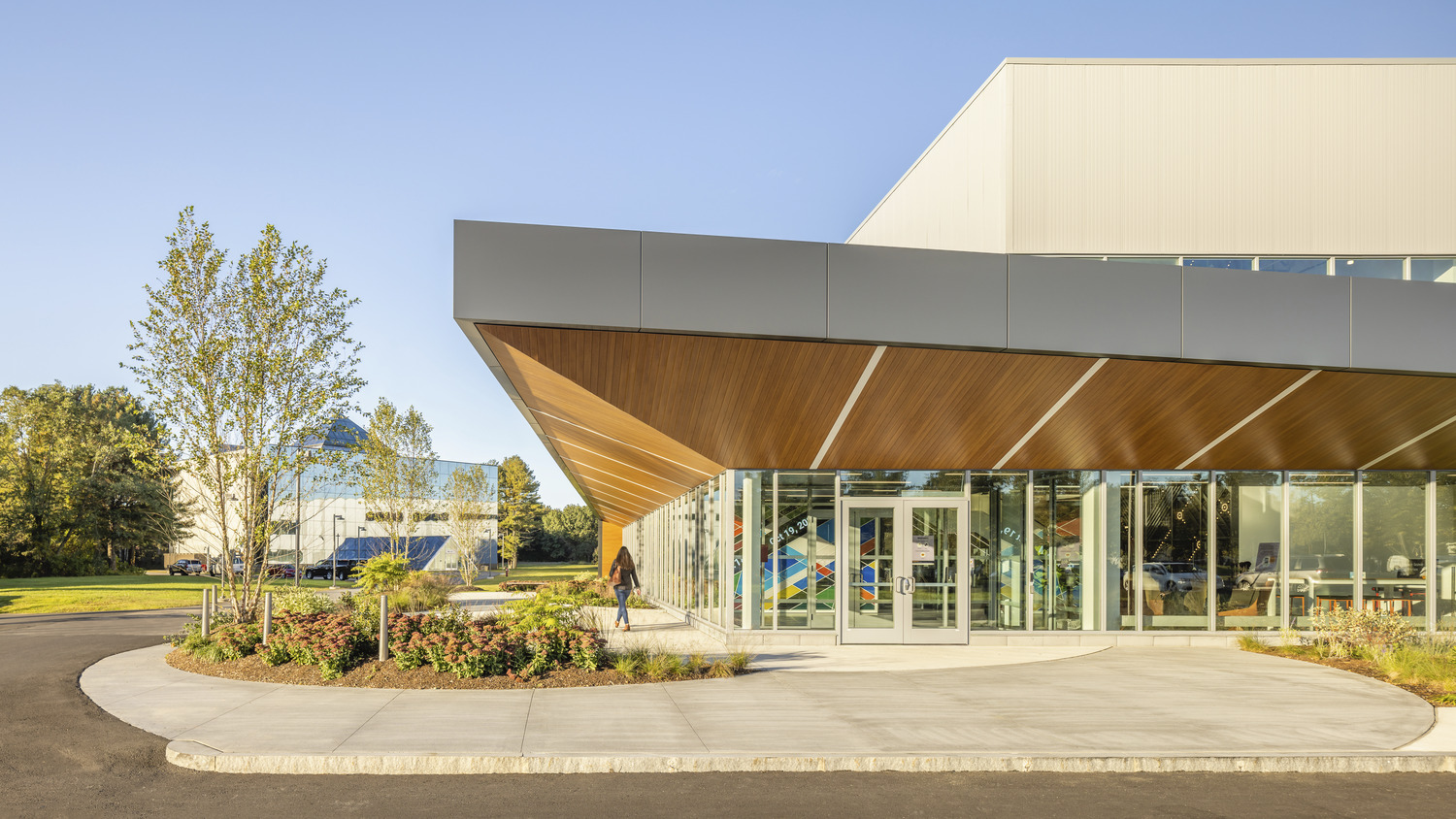
The building’s main entrance is a simple, wood-clad pavilion at the south-east corner. “We wanted it to be a really warm and welcoming experience for employees,” says Pardek. “We didn’t see it as just a door. It’s part of an experience: you’re coming from parking your car, you’re walking up the sidewalk past the larger part of the building, and now you start to be visually more interested in the front door, the canopy.”
“I love doing things efficiently, but still finding that magic so that when employees are interacting with the building, they’re not just interacting with a big box.”
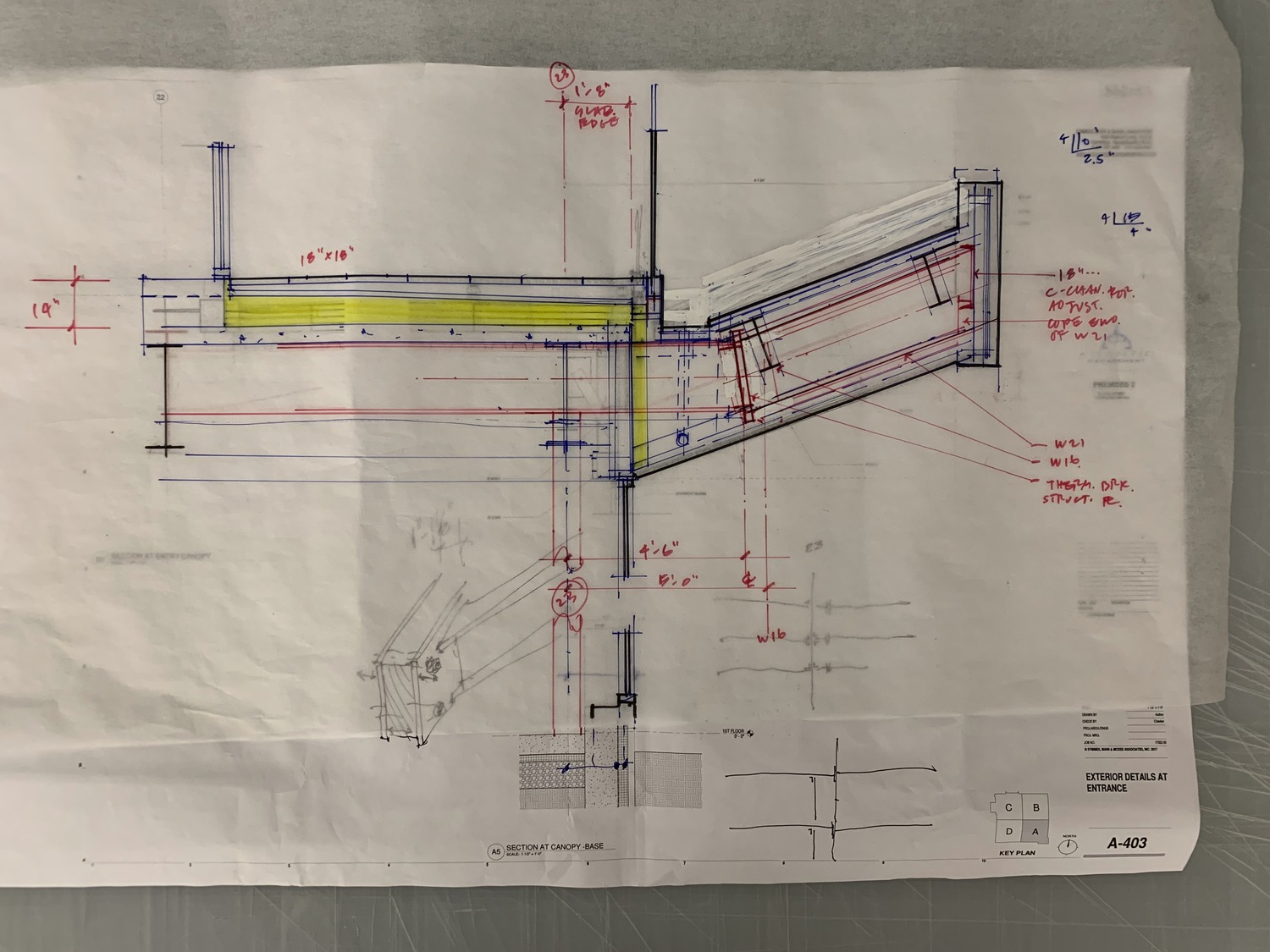
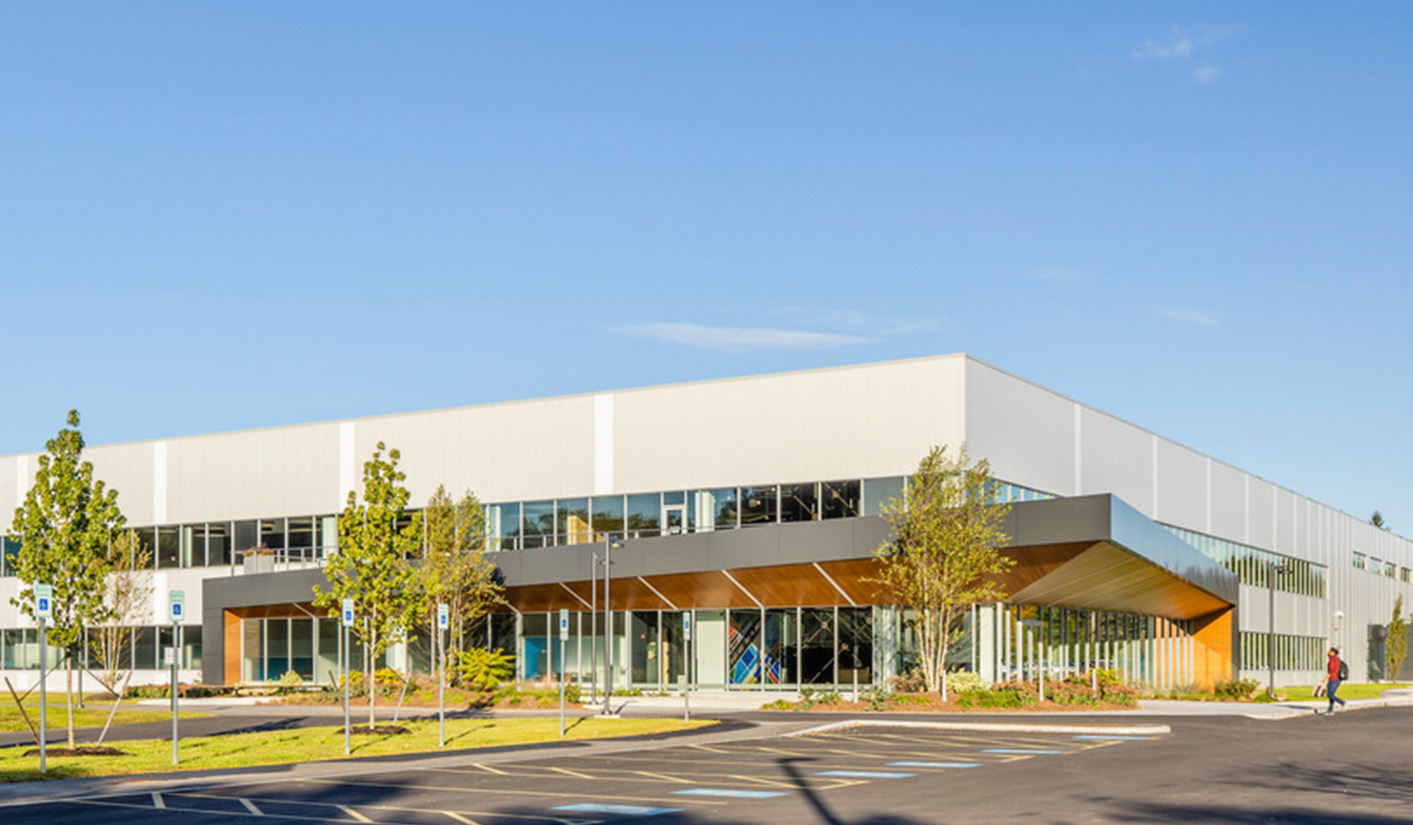
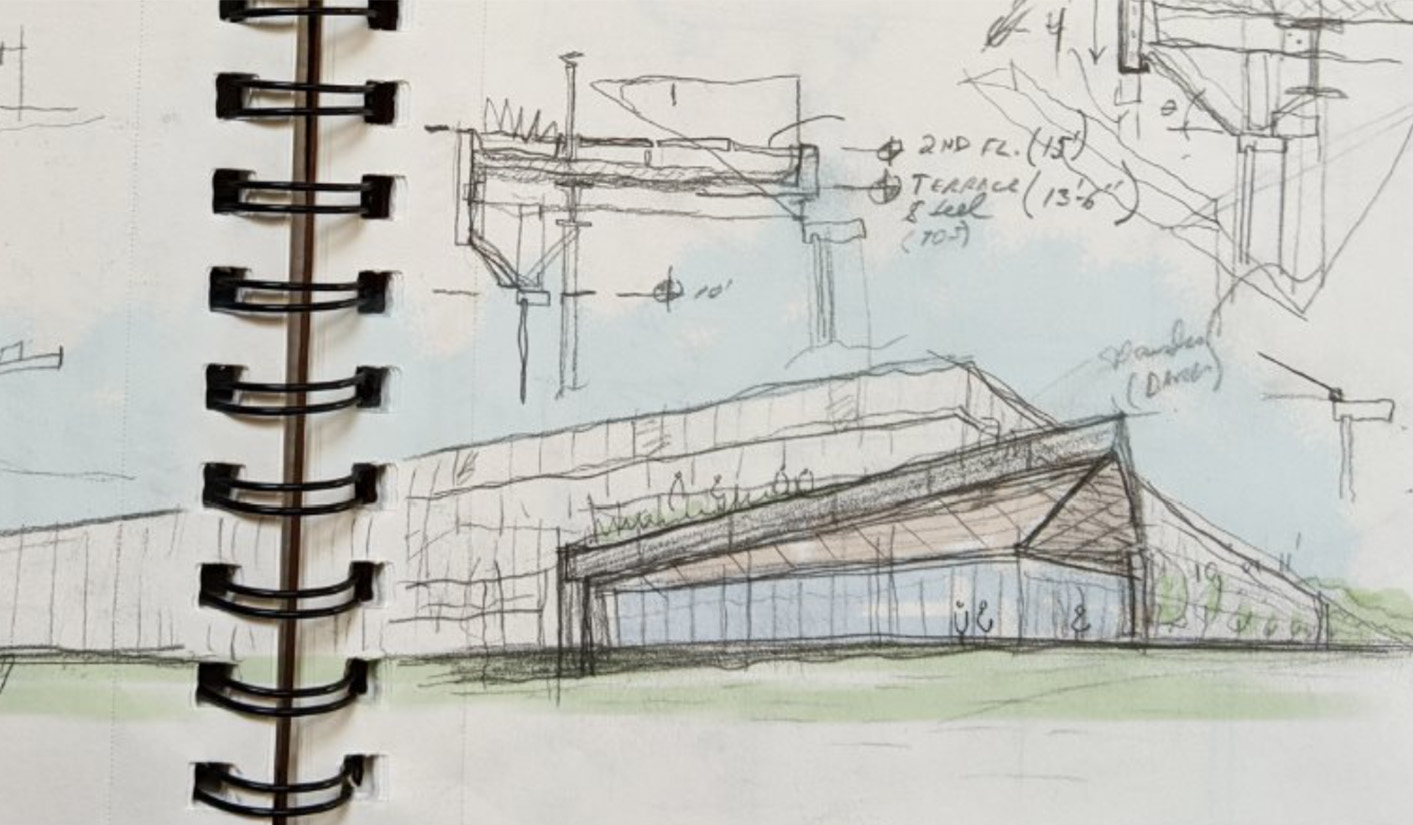
Civil solutions for a complex site
To meet the project’s tight deadlines, SMMA’s civil engineers had to accommodate Amazon’s vast new footprint while keeping permitting delays to a minimum.
“We challenged ourselves to come up with an efficient, cost-effective solution that built upon the infrastructure that was already there,” said Park. The team modified and reset the site’s existing utilities, including water, sewer, and drainage. This involved shifting an entire utility corridor from underneath the new warehouse extension, relocating it 100 yards east.
Stormwater management posed another challenge. The original AstraZeneca campus was built to 1980s stormwater regulations—now out of date. Any new development would have to meet tough new standards for groundwater recharge.
The team had to find a way to capture, treat, and discharge the vast amount of water collected by the new building’s 357,000 square foot roof. The solution: a carefully directed drainage route connecting the roof to a subsurface recharge system, with treated water filtering out into Hocomonco pond.
Facing the future
From the outset of the project, both Amazon and Atlantic Management had an eye on the long term. For Amazon, this meant keeping the option to relocate its robotics testing program to a future location, should the need arise. To this end, the team designed a demountable mezzanine that could be taken down and moved to a new building.
The three-story mezzanine was an ideal stage for Amazon to display and test their robotics equipment. But making it demountable posed an engineering challenge: how to retain the seismic soundness of both the mezzanine and the overall building?
A solution was found by designing a shared brace between the mezzanine and the building that could continue to serve as a brace after demounting the former. This bracing stabilizes both the main structure and the mezzanine in the case of high winds or a seismic event.
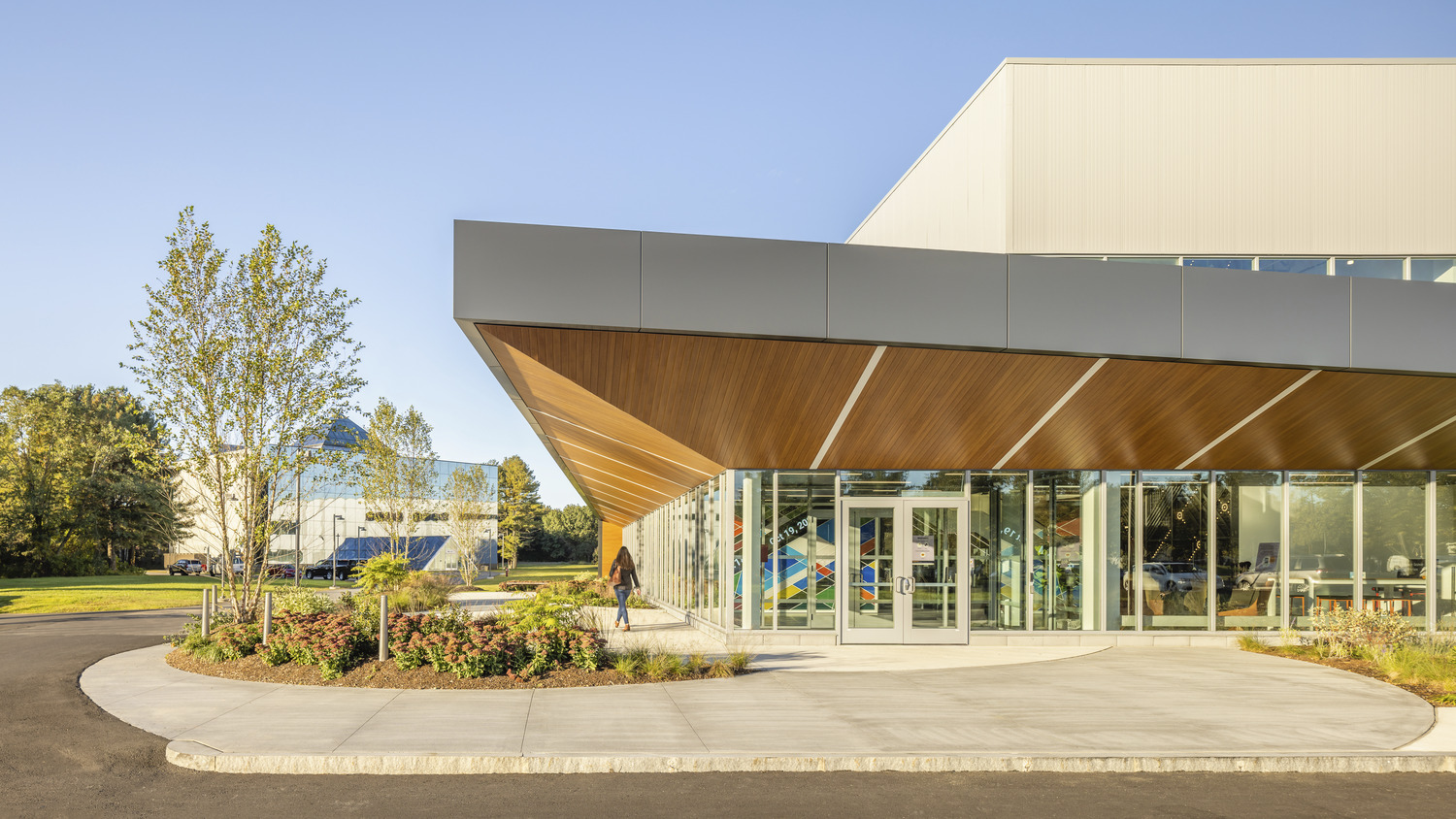
Five years after the first shovel in the ground, Amazon now occupies three large buildings at Otis Street, with each core and shell designed by SMMA. The campus stands as a testament not only to the strength of SMMA’s integrated design model, but to the success of a decades-long relationship between design firm and developer.
“I think Atlantic Management was attracted to the Otis Street project because it was really in their wheelhouse of redevelopment,” says SMMA’s Brian Lawlor, the project director. “They came out of their experiences at Lexington and Marlborough, and they knew they had the expertise on the development side, the construction side. And they knew they’d be able to successfully work with the community."
“They think win-win: How can it be successful as a development? How can it be successful for the Town, the neighbors, the community? How can it benefit natural resources? So they really do think about how this can work for everyone. And they always follow through on their commitments.”